Introduction
Quality Control vs. Quality Assurance
When it comes to maintaining product quality, two important terms come to the fore: Quality Control (QC) and Quality Assurance (QA). We often seem to associate these two tasks with one another, but they are separate and complementary processes that ensure that the quality of food, pharmaceuticals or any manufactured product meets required standards.
Imagine, if you are running a food manufacturing business, you would want to prevent any defects before they occur, and if a defective product is produced, it should be caught before it reaches consumers. This is where QA and QC come into play
Did you know? According to the Food Safety and Standards Authority of India (FSSAI),In 2022, nearly 13% of food samples failed quality tests. That’s not just a number—it’s food people trusted. Strong QA and QC ensure what we eat is safe, so families don’t have to worry about what’s on their plate. lets see (Quality Control vs. Quality Assurance)
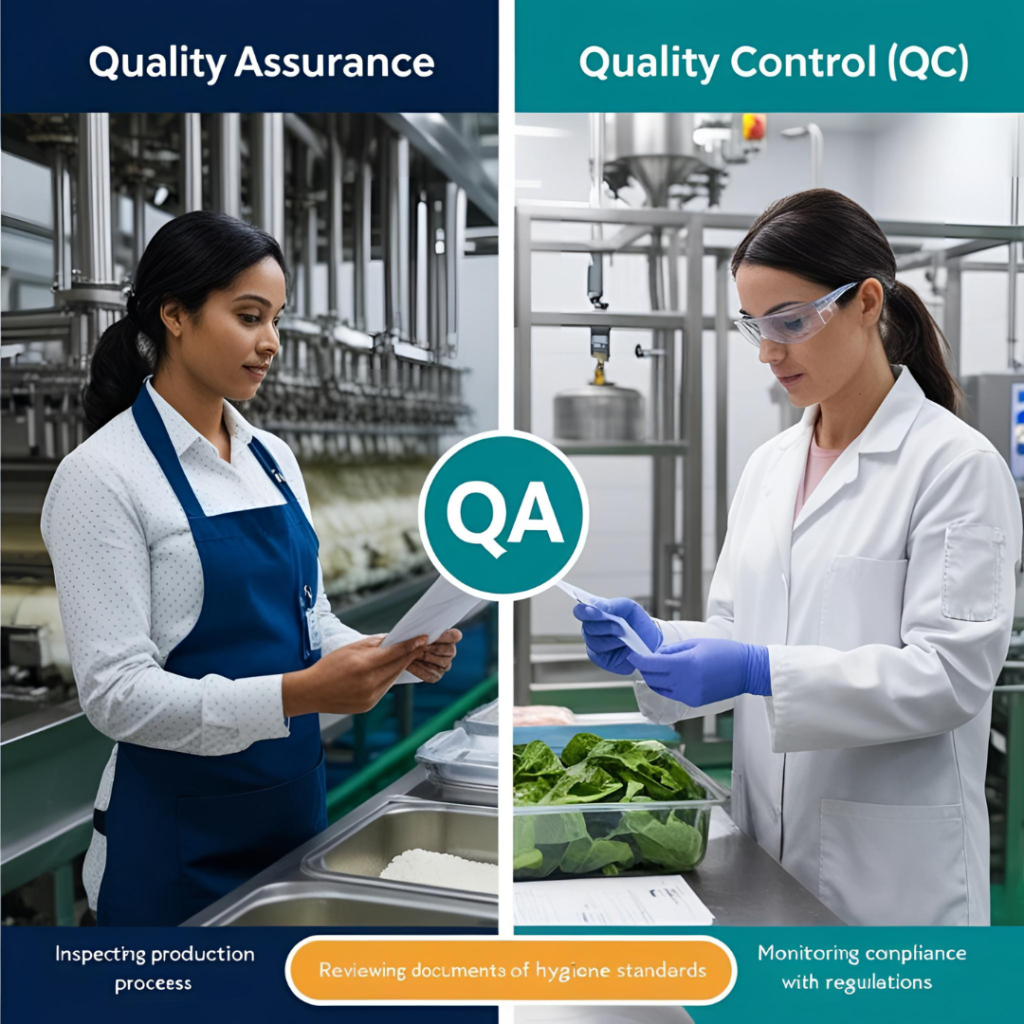
What is Quality Control (QC)?
Definition of Quality Control
Quality Control (QC) focuses on inspecting, testing, and verifying products to ensure they meet the required quality standards. It is a reactive approach, meaning it identifies and corrects defects after they occur, but before the product reaches consumers.
Key Responsibilities of a Quality Control Specialist
- Inspecting products at every stage of production
- Detecting defects and conducting tests and measurements for them
- Identifying and reporting quality issues
- Ensuring compliance with industry rules, safety standards and SOPs
- Finding solutions to quality problems together with the production team
- Inspecting raw materials to detect the presence of contaminants such as bacteria or pesticides
- Conducting microbiological and chemical tests on finished products
- Checking packaging to ensure there are no errors and that labels are printed correctly
🔹 Industry Insight: The global food safety testing market is projected to reach $32.2 billion by 2027, growing at a 7.9% annual rate, driven by stricter regulations and growing consumer awareness. (Source)
What is Quality Assurance (QA)?
Definition of Quality Assurance
Quality Assurance (QA) is about preventing defects before they happen. It is a proactive approach that ensures compliance with regulations and continuous improvement in processes. Think of QA as the system that sets the rules, while QC ensures those rules are followed.
Key Responsibilities of a Quality Assurance Specialist
A quality assurance specialist focuses on:
- Developing and implementing quality control processes
- Conducting internal audits and assessments
- Ensuring compliance with food safety standards like HACCP and ISO 22000
- Training employees on best practices
- Documenting procedures and continuously improving them
Examples of Quality Assurance in the Food Industry
- Implementing HACCP to identify and prevent food safety risks
- Auditing suppliers to ensure raw materials meet quality standards
- Establishing Standard Operating Procedures (SOPs) for food handling and production
📊 Stat Alert: Companies with strong QA programs experience 40% fewer product recalls than those without. This not only saves costs but also protects brand reputation. (Source)
Quality Control vs. Quality Assurance: Key Differences
Feature | Quality Control (QC) | Quality Assurance (QA) |
---|---|---|
Definition | Identifies and fixes defects | Prevents defects through process improvement |
Approach | Reactive | Proactive |
Focus | Product inspection | Process enhancement |
Activities | Testing, sampling, and inspection | Training, audits, and documentation |
Responsibility | QC specialists, inspectors | QA managers, compliance officers |
Goal | Ensure final product meets standards | Ensure the process prevents defects |
In Summary:QA’s job is to prevent problems before they occur, while QC checks to detect and correct any defects or issues before they reach the consumer. Both together form a strong quality management system! Quality Control vs. Quality Assurance
Why Both QA and QC Are Important in the Food Industry
- Food Safety Compliance – QA always ensures that food products follow food safety regulatory standards such as FSSAI, ISO 22000, and verifies food safety through QC testing.
- Consumer Trust – When quality is consistently excellent, brand reputation increases and customer trust remains intact.
- Cost Savings – A product is prevented from having defects before they occur, which reduces the risk of recalls and rework of the organization, and also saves money.
- Efficiency – QC catches issues as early as possible, which results in less waste and no production delays.
How do big companies like Nestlé, Unilever, PepsiCo maintain global standards by keeping their QA team always at the top level? How do these people do it? 👇
🔹 Nestlé – ensures quality by conducting audits of its suppliers and analys feedback from its consumers
🔹 Unilever – to use advanced digital systems to real-time monitor raw materials.
⚡ If we learn from these industry leaders how important product quality is, then we can take our QA and QC practices to the next level! 🚀
FAQs on Quality Control vs. Quality Assurance
1. What’s the main difference between QC and QA?
➡️ QC is reactive – it finds and fixes defects by checking quality parameters in finished
➡️ QA is proactive – it monitors and improves processes and prevents defects from occurring.
products.
2. Why is QA so important in the food industry?
✅ QA ensures that food safety protocols (SOP) are followed properly, the risk of contamination is reduced, and rules like FSSAI, ISO 22000 are followed properly. This maintains consumer trust and food safety
3. How does HACCP fit into QA and QC?
🔹 HACCP is a preventive approach system, which is a part of QA.
🔹 Monitoring and verification of critical control points comes under QC.
4. Which industries rely on QA and QC?
🏭 Food manufacturing, pharmaceuticals, cosmetics, automotive, electronics—they all follow QA & QC to ensure quality and safety.
💡 Bottom Line: QA and QC together create a strong quality system that enhances product safety and brand trust! 🚀
Conclusion
Understanding the difference between QA and QC (Quality Control vs. Quality Assurance)is very important for every industry, especially in the field of food safety and manufacturing. QC’s job is to find defects in the product and fix those product defects, while QA ensures that they do not allow defects to occur in their products. Both together ensure that the products are safe, high-quality, and regulatory compliant.
What is the role of QA and QC in your industry? Comment or share this article. this is overall information about Quality Control vs. Quality Assurance
About the Author
Vaibhav Deshmukh A food quality & safety expert with over 5 years of experience in HACCP, GMP, and quality control. Connect on LinkedIn for more insights on food safety, compliance, and quality management! connect me on Linkedin
if you like this article so please read our other related articles about food safety
food-safety-management-system-guide
fssai-license-renewal-online-process-fees-required
Pingback: Small Food Packaging: Benefits, Types, and Best Practices for 2025 -
Pingback: Quality Management System (QMS): A Complete Guide to Implementation & Benefits